For the best results in careers such as healthcare, manufacturing, technology, service industries, and pharmaceutical companies, you must learn Six Sigma, Lean, or Lean Six Sigma. Such processes are integral to business performance, quality of products, employee morale, and decreasing the variation process.
Organizations lean toward strategies or processes that positively impact their operations. Learning these agile project management methodologies can therefore land you a better position or a new job. This guide will help you decide whether Lean, Six Sigma, or some combination is the best process for a business to implement.
What Is Lean?
Lean is a set of management practices that aims to improve efficiency and effectiveness by eliminating waste. Now a standard business methodology, this approach started as a revolutionary manufacturing process in the 1950s. At that time, the main Lean principles were respect for people and continuous improvement.
According to Toyota, the seven kinds of waste in Lean manufacturing are inventory, waiting for motion over-processing, overproduction, defects, and transport.
Lean also has roots in software development, where it helped optimize the software development life cycle of Agile methodology. It creates value for the customer by optimizing a company’s resources, effort, and energy. Use the Lean methodology to identify the root cause of waste, reduce waste, deliver value, and improve the production process.
In this more recent incarnation, the fundamental Lean principles are value, flow, perfection, pull, and value stream. These principles are essential in reducing backlog when responding to customer requirements.
What Is Six Sigma?
Six Sigma is also a set of tools and techniques that organizations use to improve business processes. It uses statistical data to eliminate defects and waste. This data-driven process works with six standard deviations between the mean and the closest specification limit.
Six Sigma projects focus on implementing a measurement-based strategy to improve processes and reduce variation. To improve overall quality, it defines, measures, analyzes, improves, and controls processes falling below the specification guideline.
Six Sigma has a hierarchy of certifications ascending from White Belt, to Yellow Belt, to Green Belt, and finally to Black Belt and Master Black Belt. Someone with the Six Sigma certificate in Master Black Belt can become a project manager who consults on projects and offers strategic guidance to organizations.
Lean vs Six Sigma: The Most Important Differences and Similarities
There is a vigorous ongoing debate about which of the two methods is better for streamlining business processes and eliminating waste. The main aim of business owners, after all, is to improve their ability to meet customer’s expectations.
Both methods can easily eliminate waste and improve efficiency, but they do so in different ways. The differences and similarities in theoretical and practical aspects can help you select the best tool. Below are the main points to consider.
Different Approaches
Lean looks to maximize value for the customer with the smallest number of resources, whereas Six Sigma aims to achieve high customer satisfaction by minimizing costs.
Different Definitions of Waste
Six Sigma regards waste as a result of variation within a process, whereas Lean defines it as a process or activity that has no benefit to the customer.
Different Leadership
Six Sigma is highly recommended for organizations that are highly structured and use a hierarchical model of leadership. Lean is more flexible and can be used in an autonomous organization to enhance collaboration.
Different Functionality
Lean practices are most effective where maximizing customer value is paramount, as it is in software development. By contrast, Six Sigma works better in more complex environments, where decreasing variability and risk is key. These include engineering, manufacturing, sales and marketing, and customer service.
Similar Histories
Lean and Six Sigma both had their starts in a complex manufacturing environment. As more and more businesses have adopted these tools, however, the objectives and goals of Lean and Six Sigma have begun to diverge.
Similar Focus on Eliminating Defects and Waste
Both of these problem-solving processes seek to eliminate waste and defects. Lean and Six Sigma can contribute to the general improvement of any business process.
Similar Attention to Quality and Efficiency
They both can improve quality and efficiency by controlling costs, eliminating waste, and creating flow in the production process.
Similar Emphasis on Customer Satisfaction
They both help in augmenting the quality of a product, which in turn helps to satisfy the customer. Businesses can use either of these tools to foster brand loyalty.
Lean vs Six Sigma: Pros and Cons
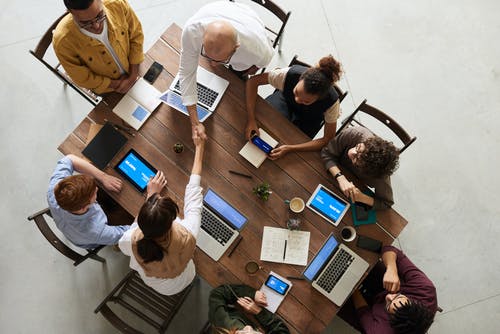
The Lean vs Six Sigma debate is prevalent in the business world. The two systems are integral to eliminating waste and creating efficiency. However, they take different approaches to achieving the same goal. The following pros and cons will help you gain a better understanding of the processes and decide which is more suitable for your business.
Lean Pros
- Simplifies processes. Lean makes complex processes more straightforward. Instead of employing many highly-skilled workers to perform a task, organizations can use Lean tools for process improvement.
- Increases speeds. Customers can’t wait for your services and products. In the age of the Internet, customers can tarnish your brand with one bad review. You can use Lean to minimize delays and keep your customers happy.
- Minimizes Inventories. Lean is a great way to control inventory. Too much inventory leads to more expenses, and less inventory leads to inadequate production.
- Eliminates Faults. Lean is efficient in reducing or eliminating any mistakes from the production process.
- Improves Flows. Lean tools are available to streamline specific processes and significantly reduce bottlenecks.
Lean Cons
- Lacks statistical tools. Lean does not have any statistical tools to control variations of the processes.
- Lacks flexibility. Lean is slow to react to new conditions or circumstances.
- Congestion. Lean’s delivery causes congestion in the supply chain, causing delays, pollution, or a shortage of human resources.
- Lacks versatility. Lean does not apply to all industries.
Six Sigma Pros
- Facilitates standardization. Implementing Six Sigma successfully can lead to many gains, including increased sales, stock value, and customer satisfaction.
- Adds value. Six Sigma improves the general output of the company. It can optimize supply chain processes and enhance customer satisfaction.
- Minimizes waste. Through Six Sigma, companies can identify variance before production. This helps in lowering the cost of operation and creates opportunities for learning. Experts can analyze the documentation to gain insight into the business processes and their efficiency.
Six Sigma Cons
- Long Implementation Time. It requires the involvement of every employee to implement. This may take a lot of time, especially in a big organization.
- Limited Functionality. It is only suitable for specific industries.
- Complicated. Businesses require large amounts of statistical and empirical data to be analyzed for variance. This can be time-consuming and complicated.
- Costly. Six Sigma improves costs in the long run. However, the repetitive nature of its processes can increase overhead and operational costs.
Should You Use Lean or Six Sigma?
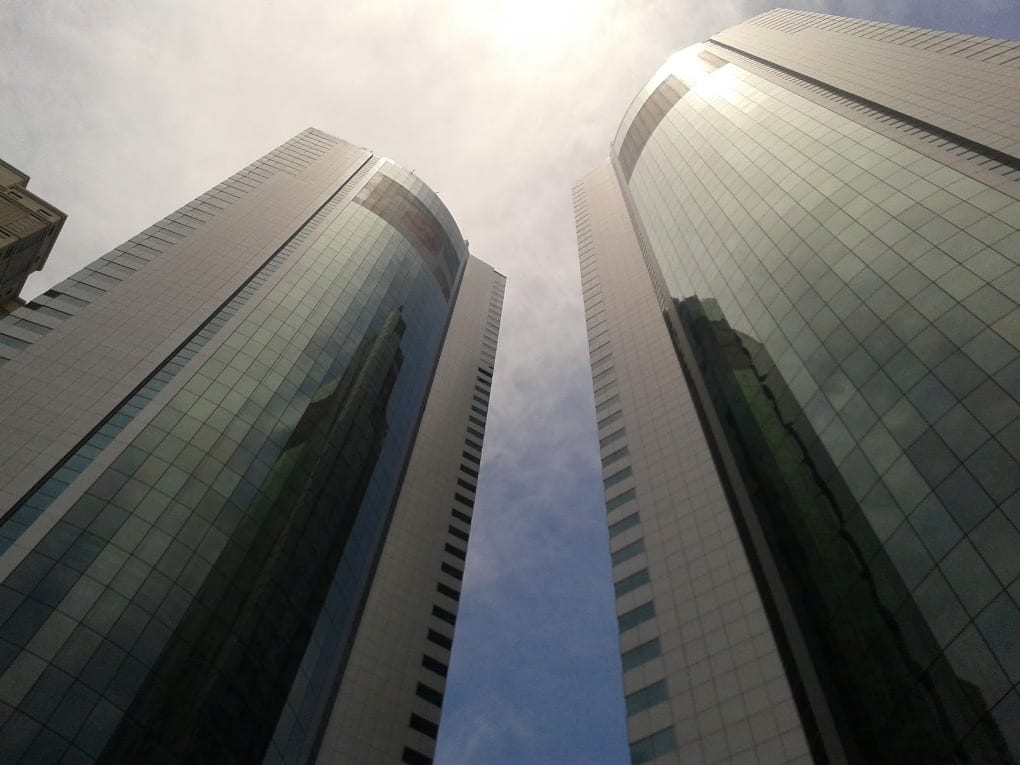
Six Sigma and Lean both have proven track records, especially in manufacturing. For a company that works extensively with artificial intelligence, Six Sigma can prove most beneficial, whereas an operation heavy in human resource management will benefit most from Lean.
However, companies do not have to choose one over the other. They can combine both processes and improve their production models.
As you start a new company or new enterprise, Six Sigma should come before Lean. Six Sigma delivers the best possible product to the customer with minimum variation. Implementing Lean will ensure maximum efficiency, but it may deliver an unusable product in the short-term.
Use Six Sigma in cases where your process has too many variations and has not been delivering what the client needs. You can use Lean to ensure that the customer gets what they want in the long run.
Advantages of Choosing Lean
Using Lean can maximize your organization’s profits significantly. You can use the practices to reduce costs and increase savings. In addition, it helps improve the culture of the organization. Workers become more focused on daily improvement, making their work more impactful.
It also boosts the employees’ morale by making sure they are in constant communication with their bosses.
Advantages of Choosing Six Sigma
Through Six Sigma methodologies, companies can upgrade and improve quality control. This positively impacts the quality of products and consequently enhances customer satisfaction and brand loyalty.
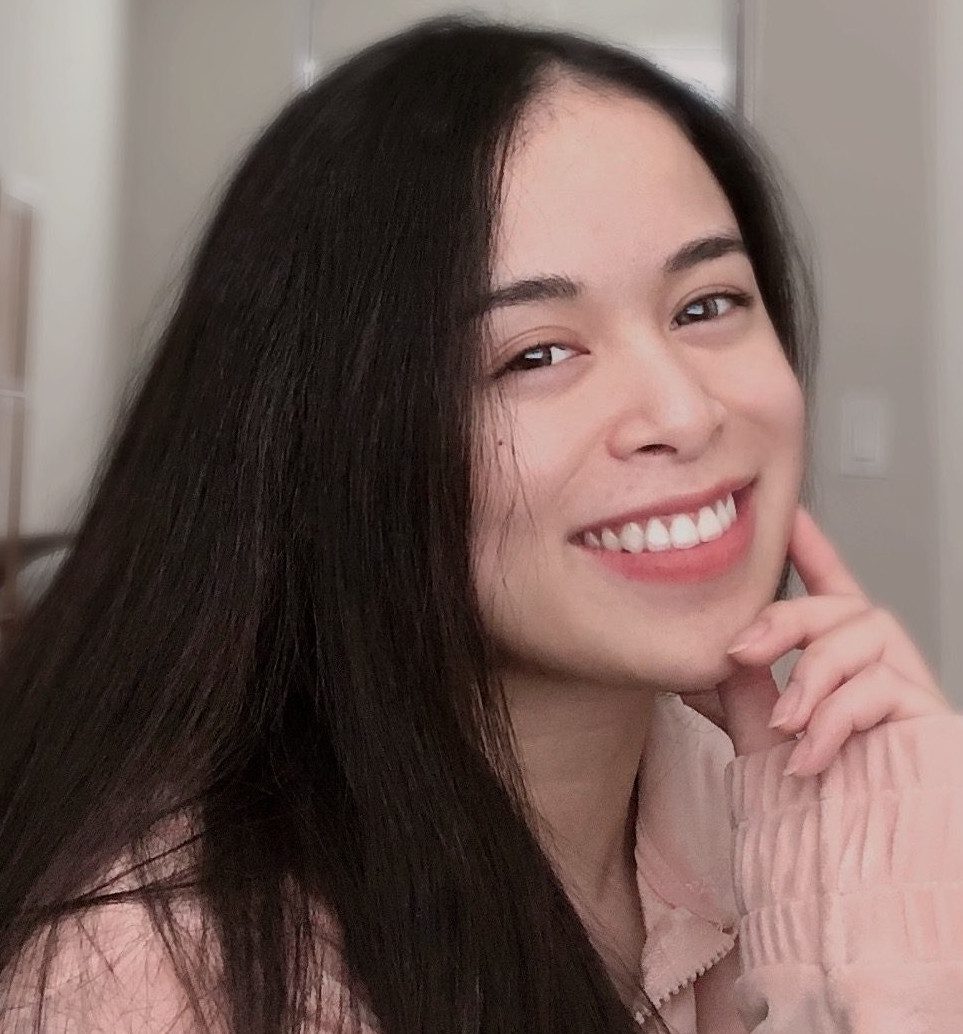
"Career Karma entered my life when I needed it most and quickly helped me match with a bootcamp. Two months after graduating, I found my dream job that aligned with my values and goals in life!"
Venus, Software Engineer at Rockbot
With Six Sigma, the feedback that employees get from their bosses can also lead to a greater sense of unity. Six Sigma has a proven track record of value-added processes and high-quality production.
About us: Career Karma is a platform designed to help job seekers find, research, and connect with job training programs to advance their careers. Learn about the CK publication.